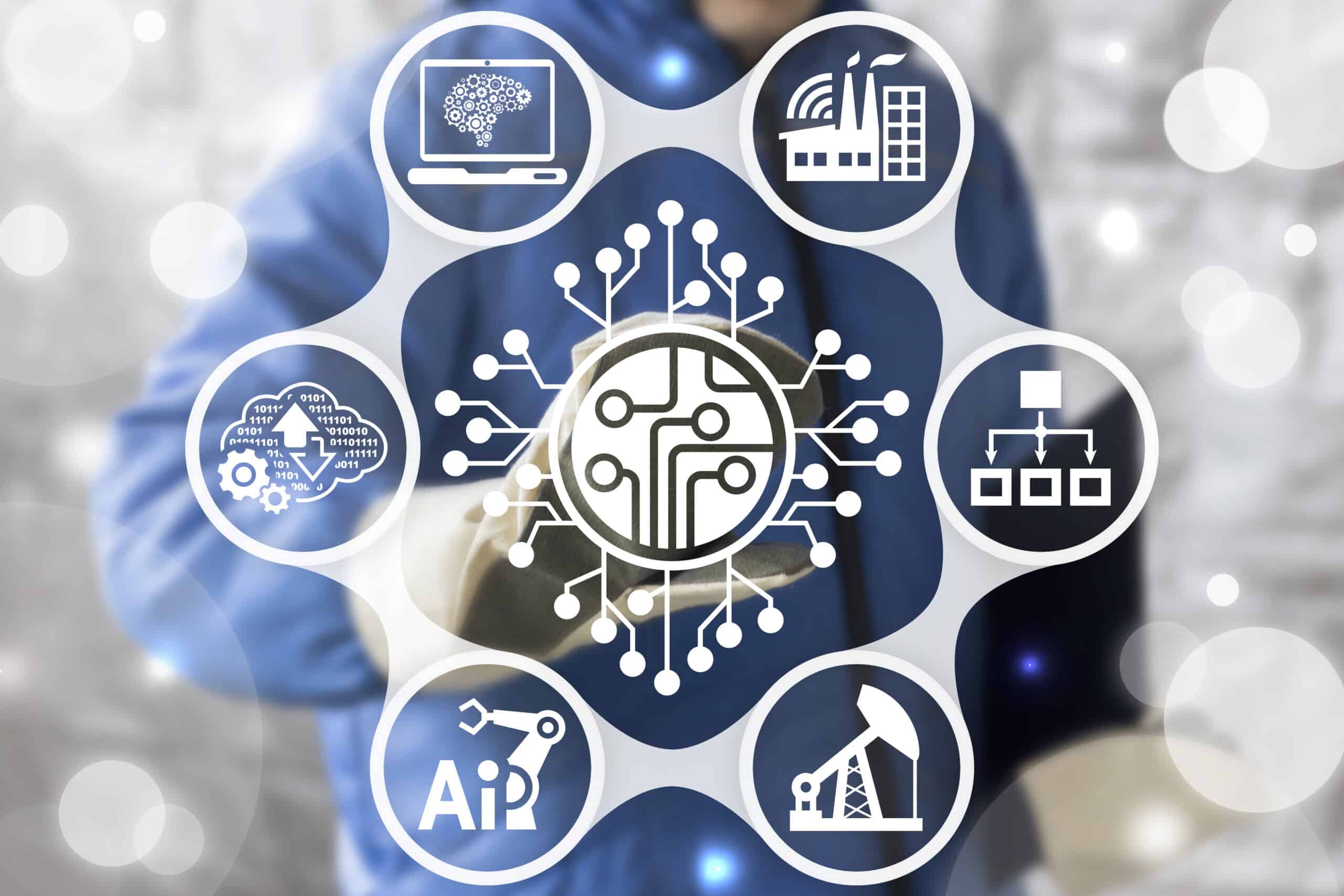
Blog 3: The Everyday Superheroes Tackle Compliance
Deep in the Southwest, a public utility is responsible for keeping millions of people’s lights and power on in one of the hottest cities in the country. An outage can be catastrophic – putting immense pressure on utility leaders who know their operational efficiency is literally a matter of life or death.
That utility is Viddaco,* and you can learn the back story of their digital transformation journey in Editions 1 and 2 of our “Everyday Manufacturing Superheroes” series. You’ll find out how these leaders put on their metaphorical capes to solve stubborn data challenges and modernize their operations and infrastructure. Their new digital superpowers were so effective they surprised their entire team – but they hadn’t yet tackled their compliance headaches, which brings us to today’s installment.
So far, Bruce, Viddaco’s engineering manager, launched a Digital Asset Transformation Model (DATM) engagement that transformed their processes, their technology, and their workforce. Data scientist Selina worked with the consultants to create a unified data source that gave every worker access to accurate, current information. After running into trouble on a facility acquisition project, Diana used Kinsmen Group’s data transformation tools and service to identify missing equipment documentation with AI – something that gave her a clean data set for all equipment and saved the company hundreds of thousands of dollars.
The team felt pretty good about themselves. Once haunted by the repercussions of a potential power failure, Bruce could already see how much more efficient the sites were, and Viddaco’s ongoing quest to modernize its grid seemed much more attainable.
It all felt like smooth sailing ahead until Clark brought up their compliance and decarbonization challenges.
Simplifying Compliance Chaos
Clark had played a role in the missing documentation fiasco, overseeing compliance and safety requirements. The experience excited him about the possibilities for simplifying Viddaco’s compliance processes and assisting with sustainability initiatives. He just wasn’t sure how or if the DATM engagement with Kinsmen could pull it off.
“We have decarbonization goals to meet by 2035,” Clark reminded Bruce. “This engagement is helping us get asset information faster, which is awesome. But our teams need to collaborate better if we’re to hit our targets. And as we continue to make changes, we’ll need to see actionable insights to know what’s working and what isn’t.”
In other words, the challenge to tackle next: Compliance Chaos.
“Between our contractors, suppliers, and internal teams, everyone seems to be using different workflows and processes,” Clark said. “We have federal, state, and other regulations to meet, and preparing for audits is a nightmare because our processes are inconsistent and inefficient. We mostly have all the data for regular compliance activities, but when something happens, we are scrambling.”
Bruce and Clark gave their DATM consultants their wish list. It included:
- Conformity and consistency in all processes across different plants, teams, and systems.
- Accurate data monitoring and auditability.
- Audit trails that confirmed operational safety, asset maintenance, and documentation fidelity.
- The ability to easily organize all necessary information for FERC, NERC, CEII, and other regulations.
The Results: Faster than a Speeding Bullet
Within a few months, Clark happily reported that Viddaco’s compliance and sustainability programs were on track and at a lower cost than predicted.
“If I had to summarize our results in one word, it’s FAST,” he said. “We can get new production asset information in place faster, which means we can move quickly on transitioning our old non-sustainable equipment into environmentally friendly technologies.”
Clark also found that embedding proper document and data management processes into Viddaco’s programs yielded other benefits. Design quality improved, and the teams found collaboration easier across different locations and departments. In addition to design improvements, Kinsmen also advised on how to incorporate sustainability metrics in the equipment purchased. As a result, the facilities now have a much better handle on the expected total CO2e footprint across the whole lifecycle of the equipment, which feeds into our sustainability program.
Because DATM helped identify their most valuable data insights, Clark could accurately measure and analyze the performance of their new energy-efficient and sustainable assets.
“Any decision we make around energy efficiency and consumption is just smarter now because we can look at it from a total lifecycle point of view,” he said. “We have the data points we need to act swiftly and ensure we’re headed in the right direction in the most cost-effective way possible.”
Another advantage was the new controls and workflows, which helped Clark and his team locate asset information whenever needed.
“We can search for and find any data we need – and we have the peace of mind of knowing the data is accurate,” he said. “This is a huge lift in streamlining our annual audit preparation. As a public utility, we must meet state archival laws and FERC, NERC, and CEII regulations. In the past, that has involved significant overtime in organizing our information – and there’s always been the fear of incorrect data coming to light. But now everything is trackable, current, accurate, and easy to find. It’s been a real game changer.”
At their midyear meeting, Bruce, Clark, Diana, and Selina congratulated each other on their wins. All of them felt confident about successfully meeting the industry demands of the future, their most recent audit went smoothly, and their engineering, operations, and maintenance teams had improved collaboration and consistency. The DATM engagement had worked out better than they hoped.
What they didn’t know was that a disaster was on the way, putting all their changes to the test… as we’ll see in our fourth installment of “Everyday Manufacturing Superheroes.” Stay tuned!
*Names changed to protect their real identities.
Click here for more information on Digital Asset Transformation Model (DATM)